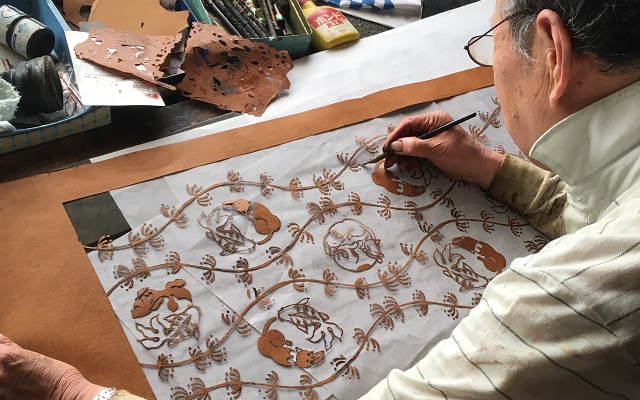
Source: KIMONO DESIGN media
Wanted: Apprentice to Last Living Expert in Shabari, Artisanal Craft Crucial to Japanese Textile Tradition. All Nationalities Accepted.
- Source:
- @atsushi800 / KIMONO DESIGN media
- Tags:
- Ise-Katagami / Kimono / Mie Prefecture / shabari / textile industry / Traditional Craft / Traditional Japan
Related Article
-
Textile maker releases woven traditional Japanese paper masks for kimono
-
Hand Painted Tumblers Combine Your Morning Coffee With Traditional Japanese Craft
-
Artist Celebrates Japanese Art and Culture With Strong and Beautiful Women Illustrations
-
Kimono Style: Celebrating in Shimoda With The Black Ships Festival
-
Shinjuku’s Isetan releases gorgeous collection of Taisho Era kimonos and accessories
-
Gorgeous flower display in Japanese botanical gardens looks like a painting come to life
In a tweet which got shared over 46,000 times, Ise-Katagami textile stencil artist and self-styled "hybrid craftsman" Atsushi Kimura sent out the following desperate plea for help:
"Isn't there anyone who would like to be the only craftsman in Japan? For shabari, a craft necessary for Ise-Katagami. The only living craftsman is here in Shiroko (a district in Suzuka, Mie Prefecture) and he's already in his late 70s. Every day, he says: "I want to quit" but he can't because he keeps getting job requests from all over Japan. Someone help!"
Ise-Katagami
Ise-Katagami (伊勢型紙), the Japanese craft of making paper stencils for dyeing textiles, was designated an Important Intangible Cultural Property of Japan in 1993 and is traditionally centered on the city of Suzuka in Mie Prefecture. The thick stencils are crafted from a special paper handmade by pasting together multiple sheets of washi, or traditional Japanese paper, with kakishibu, the tannin-rich juice of the Japanese persimmon. Many Ise-Katagami stencils found their way to Europe, together with Ukiyo-e prints, at the end of the Edo period, inspiring the japonisme movement.
source: KIMONO DESIGN media
Actually designing the stencil involves four main processes:
hori, or carving, which can be done through several cutting techniques, urabari or pasting washi paper on the back of the stencil, tsurikiri or cutting out pieces from the washi backing needed to create the pattern, and finally, shabari, or reinforcing the stencil.
Artisans skilled in the first three steps of the stencil-making process are still around, but Mr. Tanaka is the only remaining shabari artisan in Japan to practice the crucial final step, without which dye would seep through the intricate stencils, ruining the delicate textile patterns made famous in kimonos.
Shabari
Let's see how it works. To begin, Mr. Tanaka applies a thin layer of urushi, or Japanese lacquer to the carved stencil.
source: KIMONO DESIGN media
Then, with the help of an assistant (in this case, his wife), Mr. Tanaka stretches the silk meshing as tightly as possible to cover the surface of the stencil, then attaches it.
source: KIMONO DESIGN media
Next, he carefully peels off the backing paper, revealing the stencil attached to the silk mesh. This completes the first half of the shabari process.
source: KIMONO DESIGN media
The second part begins by cleaning up the tiny specks of lacquer stuck to the mesh, a time-consuming but necessary step.
source: KIMONO DESIGN media
This finally leaves a clean stencil.
source: KIMONO DESIGN media
After that, Mr. Tanaka lets the stencil set overnight in a press, and applies a coating of urushi lacquer.
source: KIMONO DESIGN media
Et voila! A finished Ise-Katagami stencil pattern ready to be shipped out.
source: KIMONO DESIGN media
Desperately Seeking An Apprentice
Mr. Tanaka wants to pass on his craft to a worthy apprentice who will devote himself or herself to the art and help this important tradition to survive and prosper.
If you want to apply, here is what you need to know:
1. Applicants of all nationalities are welcome to apply but conversational knowledge of Japanese is required.
2. The apprenticeship usually takes about three years to complete, but if you are passionate and hard-working, you may be able to complete it in one year.
3. You will be living in a sharehouse with other artisans and apprentices of other processes in Ise-Katagami stencil-making.
4. You may not be suited for the position if you have particularly sensitive skin or an allergy to urushi lacquer.
Send in your application to terakoya.kataya@gmail.com (preferably in Japanese).
If you don't intend applying for the shabari apprentice position but still want to a chance to learn more about Ise-Katagami and get some hands-on experience during your trip to Mie Prefecture, the Terakoya Isekatagami studio and school in Suzuka provides a two-day original design workshop where you can make your own yukata summer kimono, tenugui towel and cloth, as well as an "apprenticeship" workshop staying on site for four nights and five days or for six days if you have other lodging arrangements in town. Promising candidates who complete the apprenticeship workshop and are willing to commit will be offered an opportunity to become Ise-Katagami artisans.
Let's hope Mr. Tanaka finds the ideal candidate so he can finally enjoy his retirement. Who knows, his future apprentice may be reading this article right now...